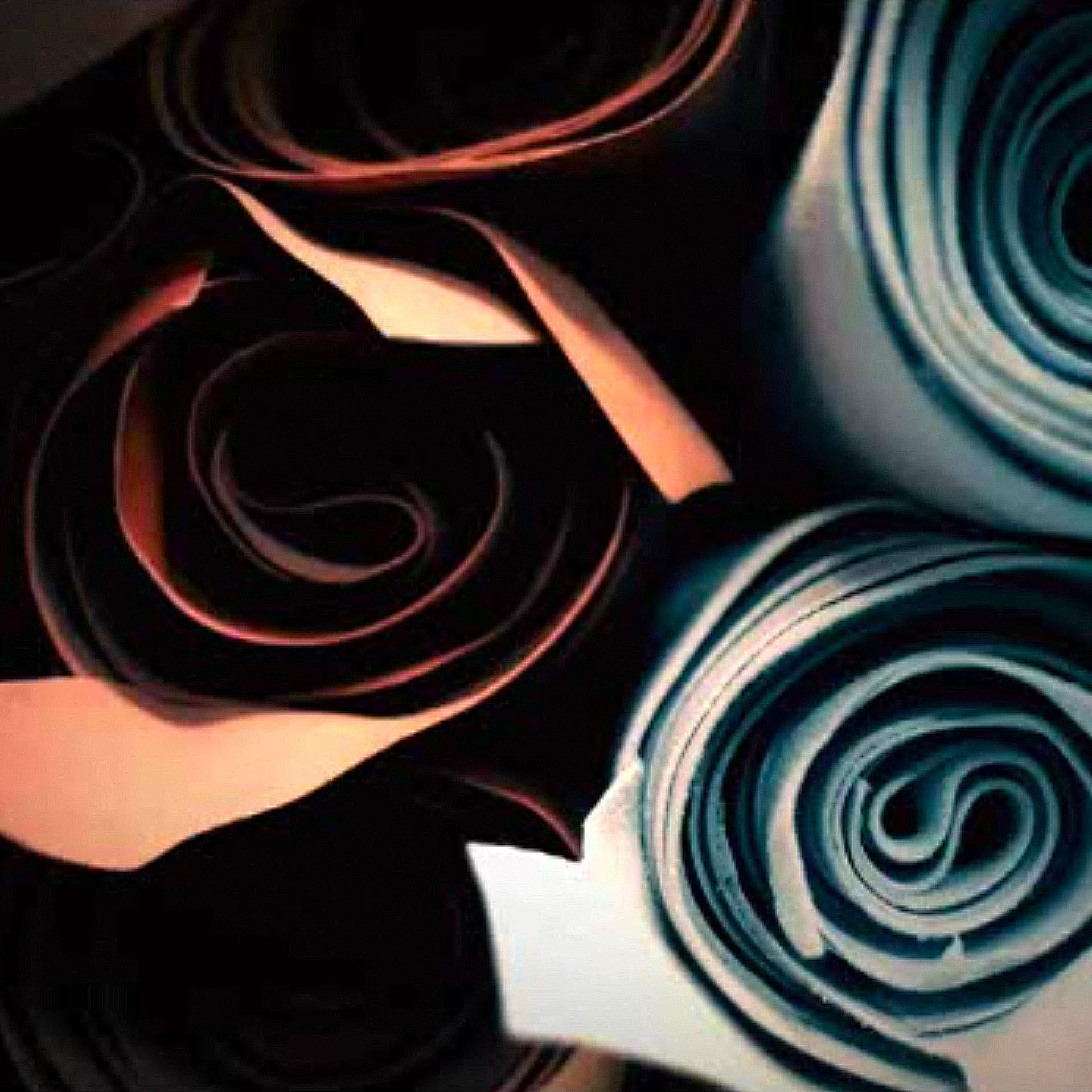
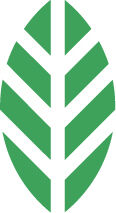
New Balance's Green Leaf Standard
New Balance’s green leaf standard indicates environmentally preferred material adoption across our footwear and apparel products. We call a material environmentally preferred based on its physical characteristics, like recycled, or based on its sustainable sourcing practices, like leather sourced from the Leather Working Group. For apparel to meet New Balance’s green leaf standard, at least 50% of the materials in a garment must be sourced as environmentally preferred. For footwear, at least 50% of the materials in the upper must be sourced as environmentally preferred and at least one material in the midsole/outsole must contain approximately 3% biobased or 5% recycled content. Apparel and footwear upper material usage is calculated by pattern area. Details of how a product meets the green leaf standard can be found on its hangtag, garment care label or its listing on www.newbalance.com.
Building our products more responsibly is an ongoing journey. We are advancing the green leaf standard by focusing on our highest-volume products, placing our efforts where the impact will be the greatest. In our Spring 2022 collection, approximately 19% of footwear volume from newly released styles and more than 60% of global seasonal apparel volume met our green leaf standard. (“Global seasonal apparel” for green leaf calculations excludes certain apparel categories: licensed products, products designed and marketed by regional design centers, New Balance direct to team and global football.)
Environmentally Preferred Materials
Choosing environmentally preferred materials is one of the most significant and immediate ways we can reduce our impacts. We are focused on transitioning our three most commonly used materials—polyester, leather and cotton—to environmentally preferred alternatives. As described above, we call a material environmentally preferred based on its physical characteristics, like recycled, or based on its sustainable sourcing practices, like leather sourced from the Leather Working Group.
Our goal is for all of our cotton and leather to be from preferred sources and 50% of our polyester to be recycled by 2025.
In 2021, 30.9% of our polyester was recycled, 92% of our leather was sourced as preferred, and 1.8% of cotton was sourced as organic. Preferred cotton sourcing ramped up in the second half of 2021 to approximately 75% preferred cotton for product being introduced in 2022, which will be reflected in our 2022 reporting. Polyester and cotton data includes textiles, labels, laces, webbing, boxtoes and counters, and most backer materials. EPM metrics and progress toward these goals excludes certain categories, like licensed product, regionally sourced materials for U.K. and Japan, global football apparel, promo apparel, and products designed and marketed by regional design centers.
More sustainable materials are continuously evolving, and we’ll keep finding new ways to have environmentally preferred materials represent a larger and larger share of our material portfolio.
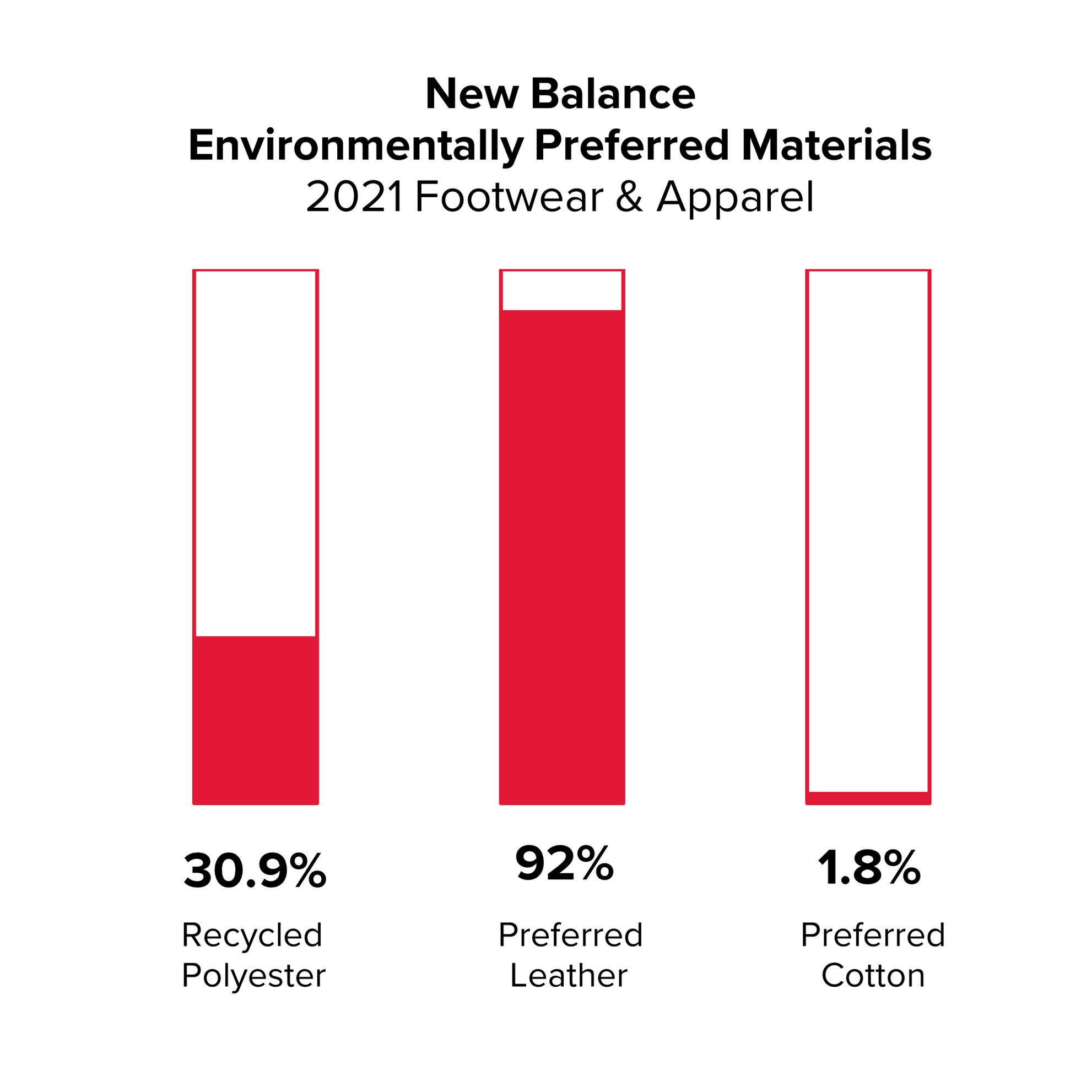
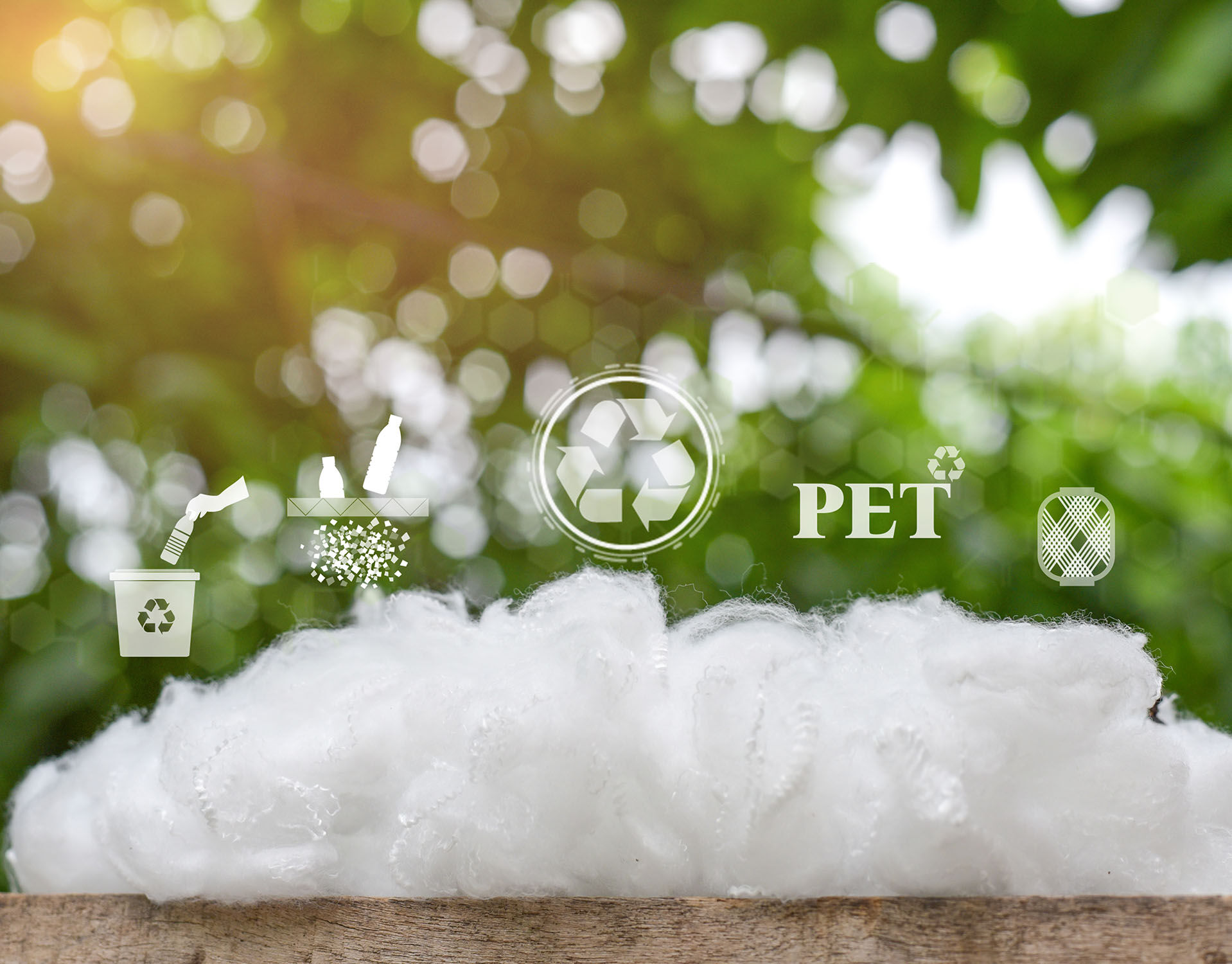
Recycled polyester can be made from recycling plastic waste into new fibers and yarns. Using it reduces our reliance on new fossil fuels, is less energy and water intensive than virgin polyester and diverts plastic waste that would otherwise end up in landfill or the environment. Integrating recycled polyester into our products is a first step to eliminating our reliance on traditional synthetic fibers. We’re accelerating this transition by focusing on products and materials that have the most polyester – both in visible elements and internal components. In 2021, 30.9% of our polyester was recycled.
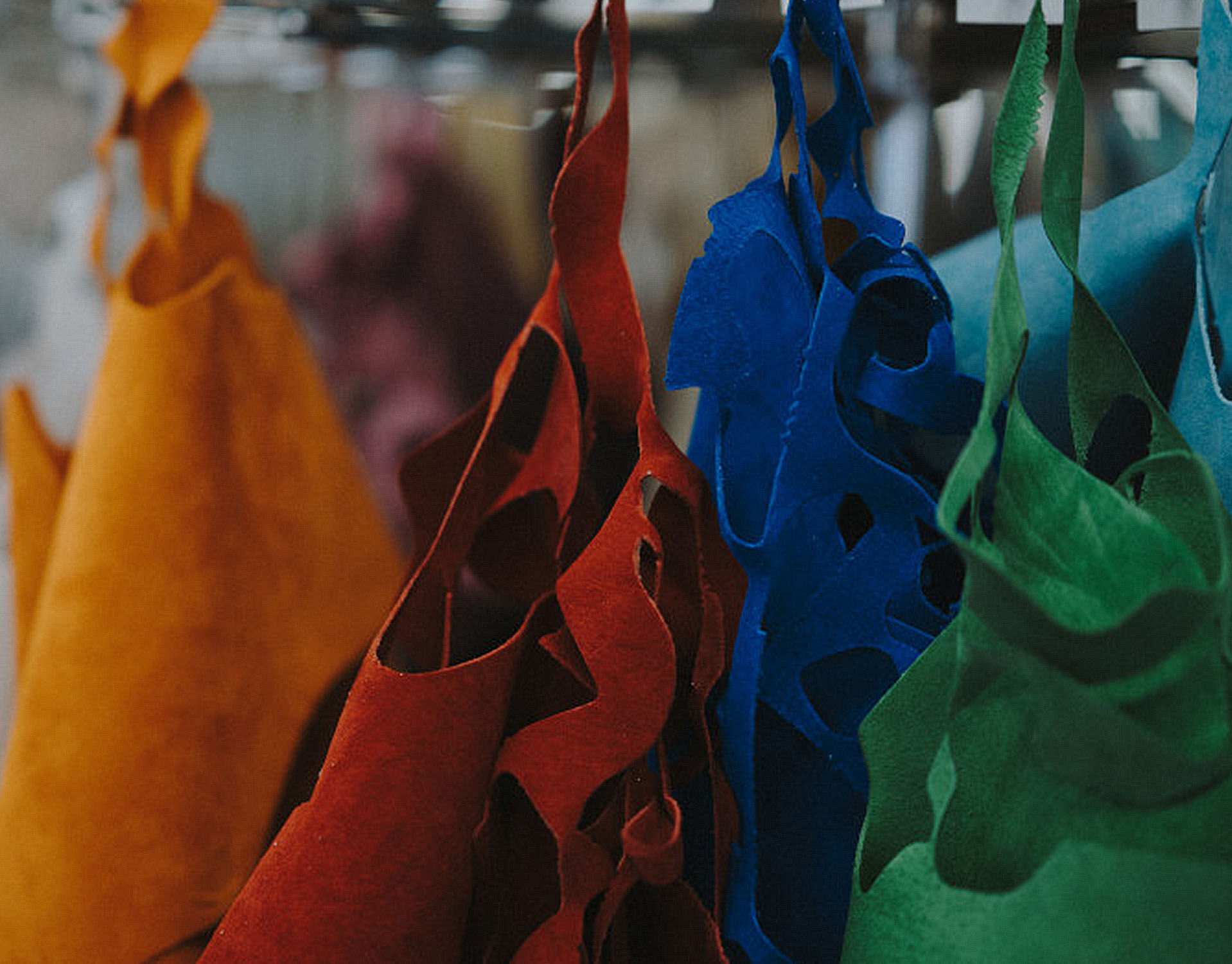
We define preferred leather in two ways: leather from Leather Working Group (LWG) Gold-rated tanneries or chrome-free leather. In addition to sourcing natural leather responsibly, we are working to further decrease our impact by exploring leather alternatives. In 2021, we sourced 92% preferred leather. Additionally, all the leather we use meets our broader Animal Materials Policy. This policy sets requirements that ensure animal welfare is protected and exotic skins are not used in our products. Our Animal Materials Policy can be found in our Restricted Substances Manual.
LWG Gold
The LWG audits and certifies tanneries based on a tannery’s ability to demonstrate good environmental practices in all aspects of leather processing production. We currently source leather primarily from Silver- and Gold-rated tanneries, and we consider leather from Gold tanneries to be “preferred.”
Chrome-free leather
Most leather is tanned with a chemical called Chromium III, which can be harmful to people and the environment if not disposed of responsibly. Chrome-free leather uses safer chemicals during the tanning process, eliminating chromium from its production.
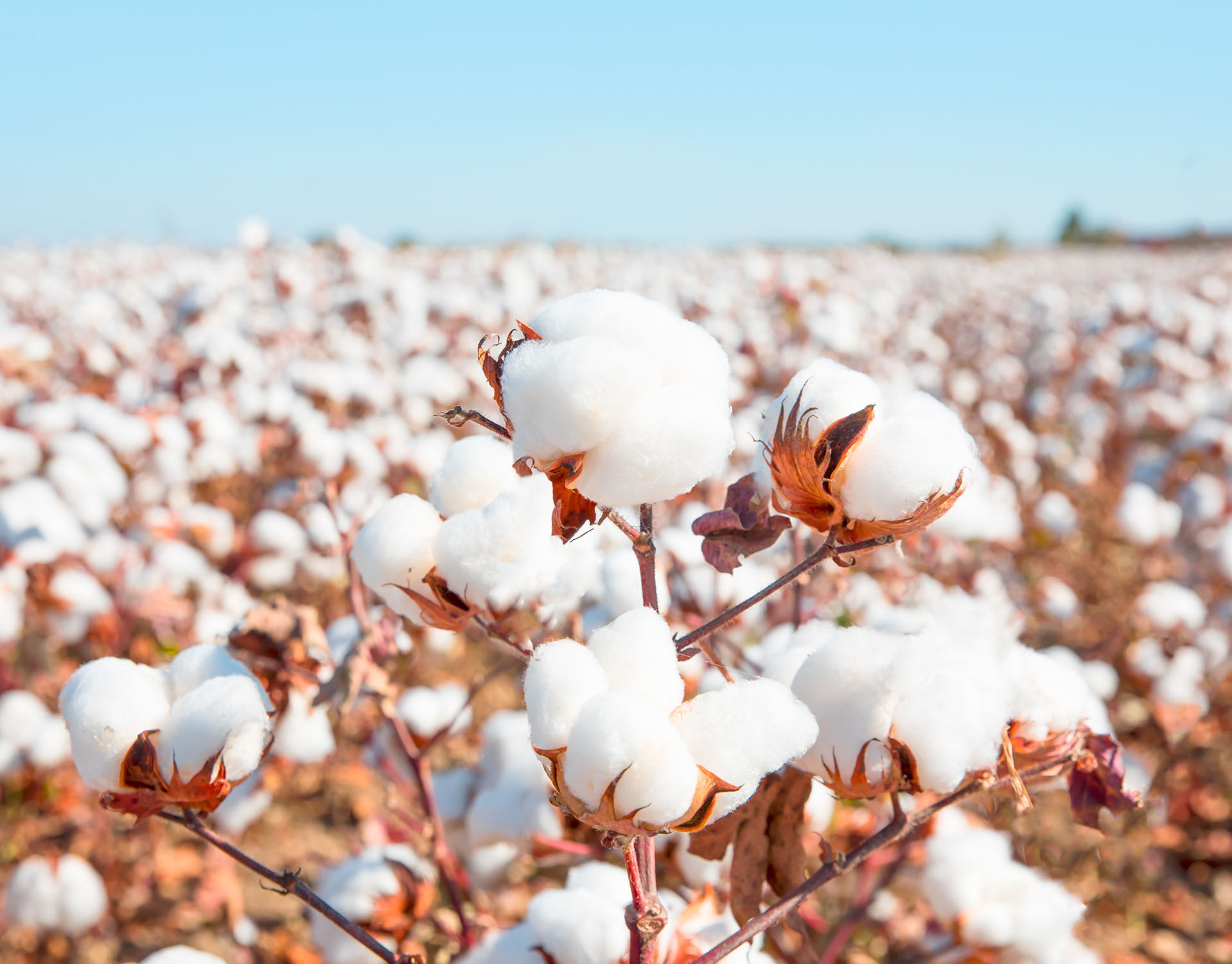
We’re in the early stages of our preferred cotton journey and we sourced less than 2% preferred cotton for products manufactured in 2021. We’re ramping up our programs to rapidly increase the percent of preferred cotton used to achieve our 2025 target.
Better Cotton
New Balance is a proud member of Better Cotton. Better Cotton is not physically traceable to end products. Buying products that were sourced as Better Cotton creates demand and directly invests in improving conditions at the farm level. Learn more at www.bettercotton.org/massbalance.
Organic Cotton
Organic cotton is grown and processed according to standards that avoid the use of toxic chemicals and maintain local soil health and biodiversity. Any organic cotton we currently use is certified according to Global Organic Textile Standards.
Preferred Soles
The majority of our sole materials are made from ethylene-vinyl acetate (EVA) or rubber. Though EVA foam provides unparalleled cushioning and rubber outsoles provide durability and traction, both EVA and synthetic rubber are derived from petroleum, and natural rubber has been linked to deforestation.
Bio-Based EVA
We are making small changes that go a long way with our EVA foams. Over 20% of new footwear in our spring 2022 launch used reformulated EVA foams that replaced approximately 3% of typical content with a sugarcane-based foam compound sourced from crops that do not compete with local food production. Sugarcane is a renewable resource and integrating it into our footwear will help reduce our reliance on petroleum.
In the coming years, we have plans to increase the amount of bio-based and lower-carbon materials used in our soles.
Recycled Rubber
Beginning with shoes launching in 2022, we are incorporating approximately 5% reprocessed rubber waste back into the formulations for many of our most used outsole materials. This innovation, which is in over 14% of newly-launched shoes, incorporates one of our factory waste streams into a closed loop system, reducing our reliance on virgin materials.
Other Preferred Materials
TENCEL™
Textiles with TENCEL™ Lyocell fibers by Lenzing are derived from renewable wood sources, providing an alternative to cotton. TENCEL™ Lyocell is produced in a closed loop process, recycling water and reusing non-toxic solvents to reduce waste. TENCEL™ Lyocell requires less energy and water than cotton and does not require the use of pesticides and insecticides.
Surplus Materials
Sometimes sustainability is as simple as using the materials you already have. In some instances, we ordered too much, the color was wrong or we used less than expected, but these unused materials shouldn’t go to waste. We are working to reduce the creation of excess materials while finding ways to use surplus materials left over from production.
Spinnex
New Balance’s Spinnex material contains a minimum of 30% surplus textile waste. The scrap textile can be any composition (polyester or cotton, for example).